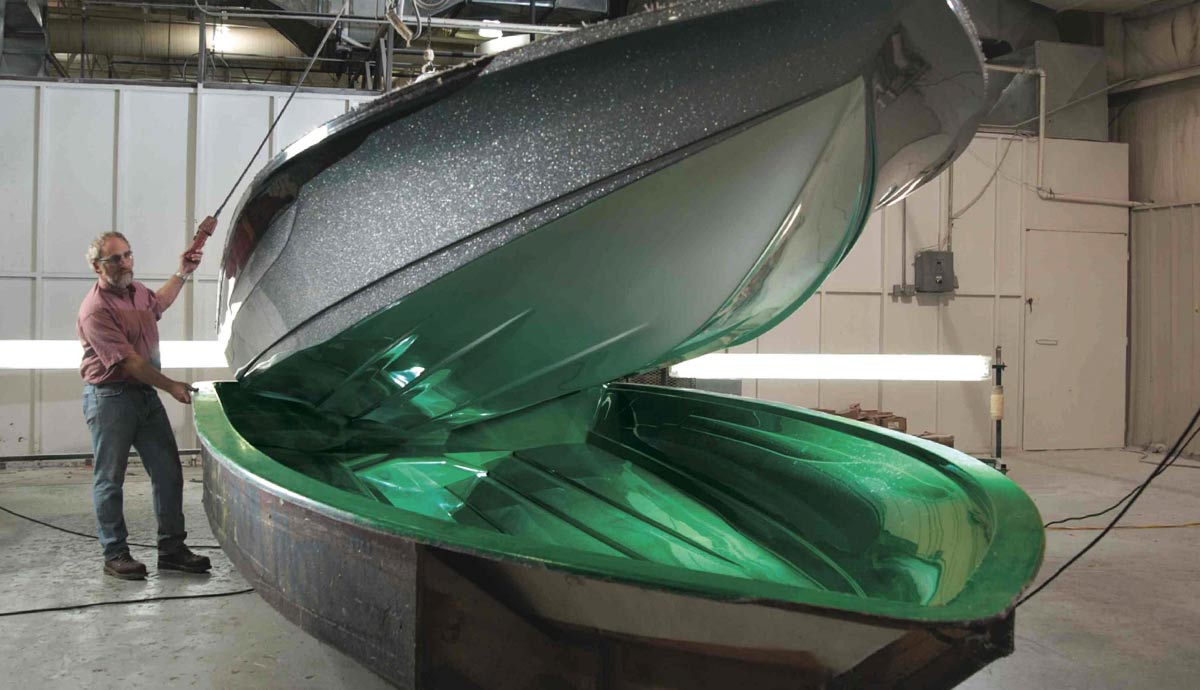
- Teknik Bülten
- 11 Eki 2023
Kalıp Ayırıcılar Kompozit Sektöründe Nasıl Kullanılır?
Kalıp yüzeyi ile ürün arasında ince bir katman oluşturarak ürünlerin kalıba yapışmasını engelleyen kalıp ayırıcılar, genel olarak kompozit sektöründe kullanılırlar ve iç ve dış olarak iki farklı sınıfta değerlendirilirler. Bu yazıda, bu malzemelerin kompozit sektöründe nasıl kullanıldığına değineceğiz.
Kalıp Ayırıcı Türleri Nelerdir?
Kalıp ayırıcı türleri uygulama alanlarına göre değişiklik gösterir. İç kalıp ayırıcılar direkt olarak reçine içine karıştırılırlarken dış kalıp ayırıcılar kalıp yüzeyine uygulanırlar. Sıklıkla kullanılan ayırıcılara bakıldığında:
• Silikon Karışımları,
• Floro Polimerler,
• Yarı-Kalıcı Kalıp Ayrıcı Sistemleri
• Metallerin Stearat Tuzları karşımıza çıkar.
İç Kalıp Ayırıcılar
Sıcak kalıp uygulamalarında reçinenin içine karıştırılmak suretiyle kullanılan iç kalıp ayrıştırıcılar genel olarak “Çinko Stereat”, “Kalsiyum Stereat” gibi formlarda karşımıza çıkar. Bu ayırıcıların temel özelliği, süreç esnasında sıcaklığın etkisiyle yüzeye çıkarak ürünün kalıptan kolayca ayrılmasını sağlamalarıdır. Tüm bunlarla birlikte fazla kullanımları belirli riskleri beraberinde getirdiğinden özellikle sonradan boyanması gereken parçalarda ve yapıştırma işlemlerinde sorunlara yol açabilir. Bu noktada kullanım oranları ve doğru kalıp ayırıcının seçilmesi kritik önem taşır. Bu ayırıcıların temel gerekliliklerine genel olarak bakıldığında özellikler arasında:
• Sistem içerisinde tamamen çözünebilmesi,
• Renge ve kürlenmeye etkisinin minimum seviyede tutulması,
• Fiziksel özelliklere mümkünse hiç değilse de pozitif etki etmesi,
• Ürün parlaklığı ve boyama süreçlerine minimum etki edecek yapıda olması yer alır.
Dış Kalıp Ayırıcılar
Dış kalıp ayırıcı malzemelerin temel özelliği kalıp yüzeyine sprey ya da uygun bez yardımıyla uygulanmalarıdır. Uygulama sonrası, kalıp ayırıcı içerisindeki solvent buharlaşarak kalıp yüzeyinde ince bir film oluşturur. Bu film kalıp yüzeyindeki mikro poroziteleri doldurarak kalıbın daha parlak hale gelmesini sağlar ve kalıbın yüzey enerjisini düşürerek kaygan bir yüzeyin oluşmasını sağlar. Bu sayede ürün ile kalıbın ayrılması çok daha kolay hale gelir.
Bu ayırıcıların temel özelliklerine bakıldığında:
• Kolay uygulanabilirlik,
• Optimum kuruma süresi,
• Kolay şekilde parlatılabilirlik,
• Maksimum ayırma performansı,
• Yüksek kalıp parlaklığı gibi özelliklere rastlanır.
Kalıp Ayırıcılar Uygulama Alanları
Ürün ile en az ürün kadar değerli olan kalıpların birbirlerinden ayrılmasını sağlayan bu ayırıcıların pek çok uygulama alanı bulunur. Pek çok farklı kalıp tasarımı bulunduğundan uygulama alanı da bu tasarımlara göre çeşitlenir. Örneğin metal enjeksiyon kalıplarında, termoset kalıbında, dövme kalıbı gibi kalıplarda ve metal form ve kesme sıvama kalıplarında sık sık ayırıcıya ihtiyaç duyulur.
Vaks Esaslı Kalıp Ayırıcılar
Vaks esaslı kalıp ayırıcıları incelerken ilk olarak polivaks kavramının tanımının yapılması gerekir. Polivaks kalıp ayırıcı serisi; yüksek ayırma gücü, parlaklık, ideal kuruma süresi, kalıplarda birikme yapmaması sayesinde ideal özelliklere sahiptir. Bu bağlamda Polivaks SV6, Polivaks SV-8, Polivaks Max-9, Polivaks N gibi ayırıcıların vaks esaslı grupta yer aldığı ifade edilebilir. Bu türden ayırıcılar sentetik ve doğal vaksların karışımından oluşturulur ve uygulandıkları alanda herhangi bir yağ, kir, toz vb. etmenin yer almadığından emin olunmalıdır. Sonrasında vaks penye bazlı temiz bir bez yardımıyla dairesel hareketler yapılarak ürüne sürülür ve yine temiz bir bez ile parlatma işleminin yapılması sağlanır. Ancak bu işlem esnasında vaksın yüzey üstünde kurumadığından emin olunmalı, çok fazla karşılaşılan bu hata karşısında dikkatli olunmalıdır. Uygulamalar arasında 15 dakika boyunca beklenmeli ve ürünlere 3 ile 6 kez uygulama yapılmalıdır. Son uygulama sonrasında hava sıcaklıkları da göz önünde bulundurularak en az yarım saat boyunca beklenmelidir. Tüm bunlarla birlikte uygulama sonrası solventin uçuşması için de beklenmesi gereklidir. Bu bekleme işlemi yeterli sürede yapılmaz veya atlanırsa ürün yüzeyinde iğne delikleri gibi delikler oluşarak ürüne zarar verebilir.
PVA Esaslı Vaks Kalıp Ayırıcılar
PVA (Polivinil Alkol) esaslı kalıp ayırıcı malzemeler temel olarak risk taşıyan, tamir görmüş, yeni oluşturulmuş model veya kalıplarda kullanılır. Yeni kalıplarda kalıp üzerindeki jelkotun aktif olduğu kabul edildiğinden yalnızca vaks yeterli olmayabilir. Bu gibi süreçlerde kaliteli bir vaks esaslı kalıp ayırıcı ile kaliteli bir PVA doğru bir şekilde ve oranda kullanılarak kalıp yapışma riskinin en aza indirgenmesi hedeflenir. PVA esaslı kalıp ayırıcının uygulamasında ilk olarak vaks esaslı malzeme kullanılmalı, sonrasında da PVA esaslı ürün 1.8 mm tabanca ya da sünger yardımıyla tek yönlü olarak sürülmelidir. İşlem sonrası bir süre PVA oluşumu gözlenmeli ve kalıptan parça alınırken delik veya gözenek içermeyen bir film görüntüsünün varlığı kontrol edilmelidir. Zira doğru uygulama yapılmadığı takdirde gereğinden ince bir PVA filmi, sebep olacağı kalıp yüzeyindeki aşındırma etkisi ve yüzeyde oluşturacağı puslu görüntüden dolayı kötü bir görüntüye yol açacaktır.
Kalıp Ayırıcıların Endüstriyel Uygulamaları
Üreticinin doğru kalıplanmış ürüne hızlı ve kolay biçimde ulaşabilmesini sağlayan kalıp ayırıcı malzemelerin sıkça kullanıldığı endüstriyel uygulamalara bakıldığında tekne yapım sektörü ve kauçuk ürün sektörlerine rastlanır. Tekne yapım sektöründeki pek çok üretici, parça ve aksesuar üretiminde kozmetik yüzeyi korumak, üretim sürecinde istenmeyen yapışmaları engellemek gibi amaçlarla ayırıcılardan faydalanır. Öte yandan kauçuk sektörü de özellikle otomotiv sektöründe sıkça kullanılıyor olması nedeniyle hata payının en aza indirgenmesi için ayırıcılara ihtiyaç duyar.