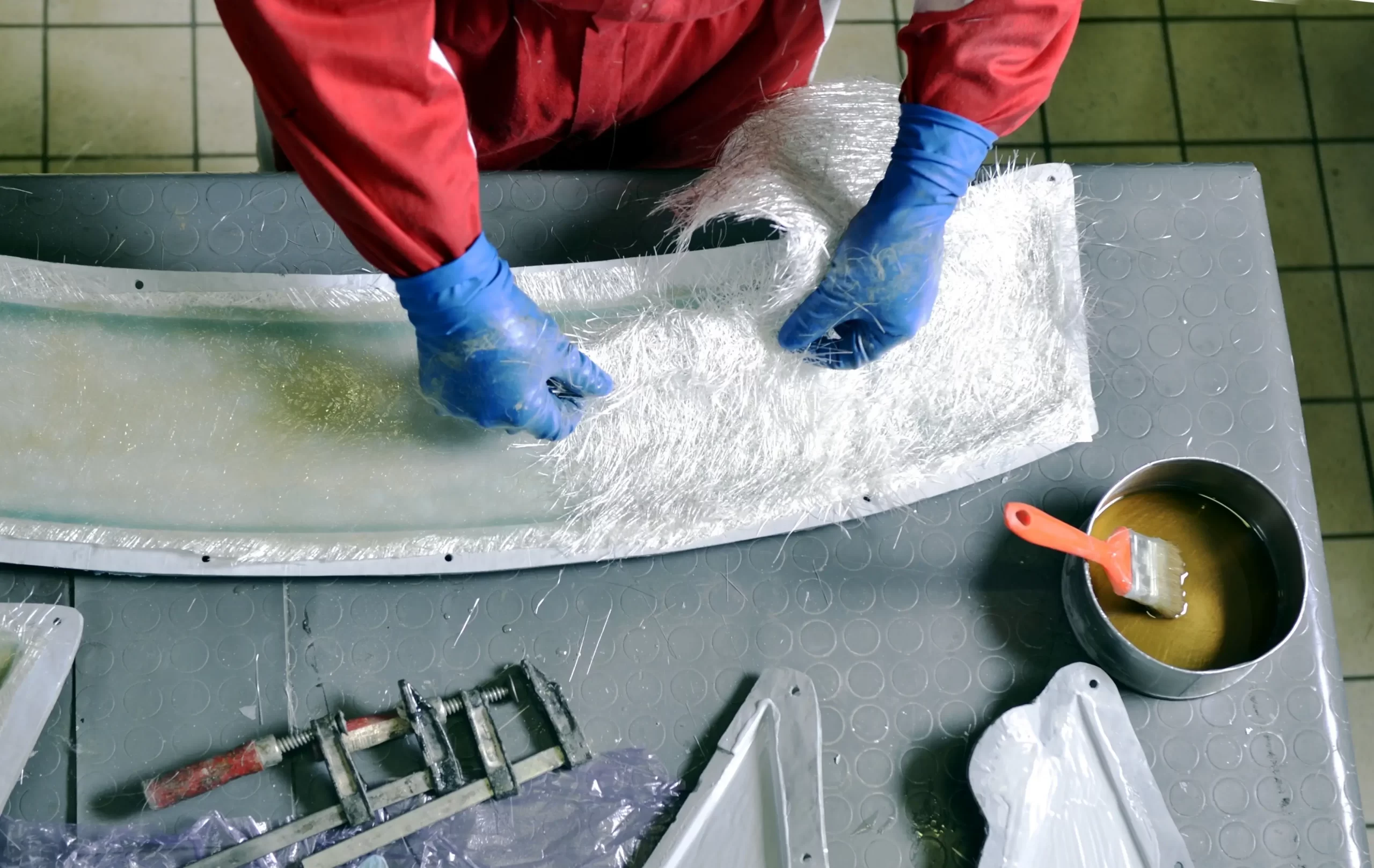
- Teknik Bülten
- 24 Ağu 2023
Açık Kalıplama ve El Yatırması Uygulamaları ve Süreçte Dikkat Edilmesi Gereken Noktalar
El yatırması, çok küçükten çok büyük ürünlere kadar geniş bir ölçekte kompozit ürünler yapmak için uygun olan açık kalıplama yöntemidir. Açık kalıplama yönteminde her kalıp başına üretim miktarı düşüktür; ancak birden fazla kalıp kullanarak önemli miktarda üretim yapmak mümkündür. En basit kompozit kalıplama yöntemi olmasına karşın el yatırması, düşük maliyetli alet yapımı, basit işleme ve geniş bir parça boyutu gibi avantajlara sahiptir. Bu açık kalıplama yönteminde tasarım değişiklikleri kolaylıkla yapılabilir ve minimum ekipman yatırımı gerektirir.
Bu açık kalıplama yönteminde ilk olarak, polimerin yüzeye yapışmasını önlemek için kalıp yüzeyi serbest bırakma anti-yapışkan ajanla işlenir. Bu ajana ‘’Kalıp Ayırıcı’’ denmektedir. Dokuma takviye tabakaları, gerekli şekillere uygun olacak şekilde kesilir ve kalıbın yüzeyine yerleştirilir. Diğer bileşenlerle karıştırılarak hazır edilen reçine, kalıba yerleştirilen elyaf takviye yüzeyine bir fırça, rulo veya spatül yardımıyla homojen bir şekilde yayılır. Daha sonra diğer elyaf katmanlar üst üste reçine ile ıslatılarak yatırılır. Hava kabarcıklarını ve fazla reçineyi uzaklaştırmak için alüminyum ezici rulolar yardımıyla basınç uygulanır. Oda sıcaklığında sertleşmesinin ardından, kompozit parça kalıp yüzeyinden çıkarılır. Kalıptan çıkarma safhasında kalıp ayırma kamaları kullanılabilir.
Açık kalıplama yöntemi olan el yatırması işleminin avantajlarını şöyle sıralayabiliriz:
- El yatırması karmaşık ekipmanlar gerektirmez, sadece basit bir kalıp ve araçlara ihtiyaç vardır, bu nedenle daha az yatırım ile daha hızlı etki sağlar.
- Üretim teknolojisi, kısa bir eğitimin ardından kolayca öğrenilebilir, ancak uzun süreli deneyim ve çalışma ile alınan sonuçlar iyileştirilebilir.
- Bu yöntemle yapılan üretimde boyut ve şekil sınırlaması yoktur, büyük gemiler veya lavabo gibi farklı şekil ve boyutlarda üretim yapılabilir.
- Aynı anda, metal, ahşap, köpük gibi diğer malzemelerle birleştirilebilir.
- Büyük tank, büyük çatı gibi bazı büyük ürünler yerinde üretilebilir.
Bu avantajların yanında, açık kalıplama yöntemi olan el yatırmasının birtakım dezavantajları da vardır, bu dezavantajlar şu şekildedir:
- Diğer yöntemlerle kıyaslandığında, el yatırmasının üretim verimliliği daha düşüktür, üretim hızı daha yavaştır ve üretim döngüsü biraz daha uzundur, bundan dolayı toplu üretim için uygun değildir.
- Makine üretimiyle karşılaştırıldığında el yatırmasının ürün kalitesi istikrarlı değildir.
- Açık kalıplama yöntemi olan el yatırmasının üretim ortamında toz ve koku bulunur.
Bu yaklaşımın kullanılmasıyla ilgili yaygın olarak karşılaşılan aşağıda belirttiğimiz sorunlardan da bahsedebiliriz:
- Yüzey kaplama reçine tabakasının zamanla çatlaması veya kırılması.
- Açık kalıplama yapılırken kalıp veya parçanın çıkarılmasından sonra yüzeyde çukurlaşma görülmesi.
- Yüzey kaplamasının bazı yerlerde mermer görünümüne sahip olması veya renk değiştirmesi.
- Laminasyon sırasında, laminasyon reçinesinin çok hızlı bir şekilde jel haline gelmesi.
- İnce kumaş ile yüzey kaplaması arasında kabarcık oluşması.
- Laminasyon sırasında, özellikle dikey yüzeylerde alttaki ana kumaşların kayması veya sarkması.
- Bitmiş laminatın arka yüzeyinin pürüzlü olması.
Şimdi gelin açık kalıplama yönteminde ortaya çıkan bu sorunları nasıl çözebileceğimize veya azaltabileceğimize birlikte göz atalım.
El Yatırması Uygulaması
Islak yatırma olarak da bilinen el yatırması uygulaması, endüstride kullanılan en geleneksel yöntemlerden biridir. Oldukça basit bir süreçtir, her bir tabaka elle tutulur ve istenilen kalınlığa ulaşıncaya kadar katman katman istiflenir. Güvenilir bir yöntem olsa da el yatırması çok fazla işçilik ve ileri imalat yöntemlerine göre daha fazla zaman gerektirir. Yöntemin kalitesi, büyük oranda çalışanın becerisine ve tecrübesine bağlıdır. Bu yöntemde karbon veya cam elyafı gibi malzemeler kullanılabilir. El yatırması yönteminde, reçineyi uygulamak ve hava kabarcıklarını gidermek ya da azaltmak için fırça ve rulolar kullanılır. Sertleşme sürecinde haricen ısı uygulanmasını gerektirmez ve genellikle oda sıcaklığında sertleşene kadar bekletilmesi yeterlidir.
Planlama
Başarılı bir ıslak yatırma süreci için planlama ve zamanlama her şeydir. Yatırma işlemini başarılı bir şekilde gerçekleştirmek ve sonuçlandırmak için, işlem öncesinde çalışma alanı, operatörlerin istedikleri her şeye kolayca ve vakit kaybetmeden ulaşabileceği şekilde düzenlenmelidir. Tüm reçineler tartılmalı, üzerleri örtülmeli ve talep üzerine karıştırılmaya hazır durumda olmalıdır. Tüm kumaş parçaları önceden kesilip hazırlanmalı ve operatörlerin rahatlıkla erişebileceği bir mesafede olmalıdır. Kalıp veya model kullanıma hazır halde olmalıdır. Yapılacak olan işin boyutu önemli bir konudur, küçük boyuttaki laminatlar için aynı anda en az iki operatörün çalışması en iyisidir ve projenin boyutu arttıkça daha fazla personel gerekebilir. İdeal olanı, her 1,25 metrekarelik alana bir yatırma operatörü ve ona reçine, kumaş ve diğer malzemeleri karıştırma ve temin etme konusunda yardımcı olan bir yardımcı personel bulunmasıdır.
Yüzey Reçinesi ile İlgili Süreçler
Yüzey kaplama (Skin Coat – SC) tabakası her şeyden önce kozmetik bir tabakadır; ancak, uygulanan belirli formüller ekstra aşınma direnci sağlayabilir. Düşük ile orta viskoziteli laminasyon reçinelerine kıyasla, Skin Coat reçineler genellikle dolgulu, tiksotropik (akışkanlığı hıza bağlı olarak artan) reçinelerdir ve dikey yüzeylerde sarkmayı önlemek için geliştirilmişlerdir.
Malzeme veri tablosuna bakarak karıştırılmış SC reçinesinin özgül ağırlığını bulun ve laminasyon yapılacak alanı kaplamak için gereken ağırlığı hesaplayın.
Karıştırılmış olan SC reçinesini tartmak, karıştırmak ve ardından karıştırılmış reçineyi ikinci bir konteynere aktararak ve temiz bir karıştırma çubuğuyla tekrar karıştırmak önemlidir. “İkili kap” yöntemi olarak adlandırılan bu yöntem, SC’nin mermerleşmesini veya renk değiştirmesini önler. Karıştırılmış olan tüm karışık partinin hemen konteynerden dağıtılması gerekmektedir. Bu, reçinenin reaksiyon süresini koruyarak kabarcıkların tamamen giderilmesi ve homojen bir kalınlık elde edilebilmesi için operatöre zaman verir.
İleride çatlak veya kırık oluşumunu önlemek ve yüzeyde çukurluk oluşması ihtimalini en aza indirmek için, SC reçine kalınlığı (0,25-0,75 milimetre arasında) kontrol altında tutulmalıdır. SC ne kadar kalın uygulanırsa, hapsolmuş havanın/gazın çıkarılması o kadar zor olur ve hizmet sırasında çekme, çatlama ve kırık oluşma ihtimali artar.
Her zaman gerekli olmasa da genellikle, arayüz kaplaması ve ilk tabakanın yerleştirilmesine geçmeden önce SC reçinenin parmak yapışkanlığında jel haline gelmesine izin verilir. Bu, kumaşın yüzeyde görünür hale gelme olasılığını minimuma indirir. Bununla birlikte, yüksek sıcaklıkta hizmet gören laminatlar için, termal döngüler yoluyla çatlama veya kırık oluşmasına karşı önlem olarak, arayüz kaplamasından sonra fiber takviyenin SC tabakasına işlenmesi tercih edilebilir.
Reçine Seçimi
Islak yatırma sürecinde zamanlama çok önemlidir. Laminasyon reçinesi için uygun sertleştiriciyi veya sertleştiricileri seçmek, operatörün reaksiyon hızını kontrol edebilmesini sağlar (kısa, orta veya uzun pot ömrü). Reçinenin kap ömrünü (pot life) ve çalışma süresini korumak amacıyla, her tabaka için hesaplanan miktarı büyük hacimli kaplarda tartın. Reçinenin yoğunlaşmaması ve hızlı bir ekzotermik reaksiyona daha az meyilli olması için bu önemlidir. Reçinenin konteynerdeki kalınlığı ne kadar ince olursa, reaksiyon hızı da o kadar yavaş olur. Karıştırılmış reçineleri spatül, rulo veya fırça ile hızlı bir şekilde dağıtarak ilk yüzeyi kaplayın, tabakayı yerleştirin, hapsolmuş havayı ve kırışıklıkları kesilmiş kıllı fırçalar veya yumuşak rulolarla giderin.
Düşük viskoziteli reçineler, kumaşı iyi ıslatırken aynı zamanda kaygan olabilir ve daha ağır tabakaların dikey yüzeylerde sarkmasına neden olabilir. Genellikle, (kalsiyum karbonat) dolgulu bir laminasyon reçinesi seçmek, kaymayı en aza indirmeye yardımcı olabilir ve reçinenin kumaş tabakasından dışarı çıkmasını önleyebilir. Kaymayı veya sarkmayı kontrol etmek için etkili bir yöntem, bir sonraki tabaka eklenmeden önce, her tabakanın kısmen jel haline gelmiş bir duruma getirilmesidir. Mesela, ilk tabaka daha kısa bir kap ömrü (pot-life), seçilerek istikrarlı (hareket etme olasılığı düşük) hale getirilir ve ardından diğer tabakalara geçilir. Burada amaç, projede en iyi şekilde çalışacak reçine özelliklerini seçmektir ve tüm laminat boyutları ve konfigürasyonları için tek bir reçine/sertleştirici sistemi uyarlamaya çalışmamaktır. Başka bir fikir ise, her bir kumaş tabakasını bantlayarak veya başka bir şekilde sınırlayarak dikey duvarlarda kaymasını fiziksel yollarla engellemektir.
Uygun Elyaf Seçimi
Üretilecek parçanın boyutu ve gerekli mekanik özellikleri doğrultusunda elyaf tipi seçilir ve serim planı yapılır. İnce dokuma kumaşlar, yüzey tabakası/tabakaları için iyi bir seçim gibi görünse de bu sıkı dokuma kumaşlar, yatırma sırasında yeterince iyi işlem görmeze ortaya çıkan gaz veya hava sıkışabilir ve Skin Coat tabakası arasında hava kabarcıkları oluşabilir. Daha düzgün bir yüzey elde etmek için yatırmanın arkasına orta ağırlıkta bir soyulabilir kumaş uygulayın. Aşırı sıkıştırmaktan kaçının. Tabakalara reçine uygularken, kumaşın iplikleri arasındaki boşluklarda bulunan gözenekli alanları en aza indirmek için hafif dokunuşlar yapın.